Use Cases
Curve H2's technology is exceptionally versatile, proficient in processing a range of hydrocarbon sources to produce top-quality hydrogen and various carbon products. This adaptability is thanks to the pioneering work of Curve H2's scientific team, who have excelled in plasma diagnostics and carefully optimized reaction parameters to prioritize hydrogen production while minimizing byproducts like methyl radicals. The unique features of Curve H2's plasma-based process are further detailed below.
Use Case 1 - Natural Gas as Feedstock
The 3-phase AC plasma reactor is designed and optimized for the treatment of hydrocarbons and the synthesis of novel grades of carbon black. The process combines the high temperature arc method with continuous gas-phase synthesis by injecting hydrocarbon gas precursors into a thermal arc plasma.
Initially an inert gas (plasma gas - Argon) is sent inside a vertical column of the reactor at a predetermined flow rate and pressure. A plasma arc is generated by the 100 kW, 3 phase AC electrode system configured at the top of the vertical column.
The plasma is powered by a 3-phase AC plasma power supply (600 Hz, 0-400 A, 263 kVA maximum power). Each of the three phases of the power supply is connected to the graphite electrodes of a 3-phase plasma torch located at the upper part of a reactor.
Thermal plasma is generated by an arc discharge between the three graphite electrodes in the plasma gas stream being used as a conducting medium.
Post the ignition of the plasma, a hydrocarbon precursor is introduced into the system at various ratios (Plasma gas/hydrocarbon gas) to get a 98% cracking efficiency with a H2 production rate of 3-4 kg/hr and 9-12 kg/hr carbon black.
Plasma density is tuned to regulate the gas temperature and methyl radical formation by controlling the input power and the partial pressure.
A quenching/sampling system collects the high temperature gas at a predetermined position, cools it down rapidly to the conditions chosen to produce fullerenes (quenching) and extracts the resulting product from the reactor.
Use Case 2 - Plastic Waste as Feedstock
Using HDPE (High Density Polyethylene) as Plastic Waste:
For the treatment of plastic wastes (HDPE pellets), a special powder injection system is employed to mix the solid carbonaceous precursor with a suspending gas to transport the mixture inside the reactor.
This aerosol flows across the plasma, reaching the highest temperature region in the reactor. Due to the high enthalpy density obtained, the plastic waste is cracking completely while passing through the plasma zone. The internal shape of the reactor has been designed to improve the conditions for cracking by a strong confinement of the gas flow.
The internal part of the plasma reactor is composed of a high temperature insulator lining (solid graphite and graphite felt) to increase the heat density as well as to decrease the thermal losses from the hot gas through the walls. The external kiln of the reactor is a double wall water cooling cylinder.
Initially an inert gas (plasma gas - N2) is sent inside a vertical column of the reactor at a predetermined flow rate and pressure. A plasma arc is generated by the 100 kW 3 phase AC electrode system configured at the top of the vertical column.
Thermal plasma is generated by an arc discharge between the three graphite electrodes in the plasma gas stream being used as a conducting medium.
Post the ignition of the plasma, HDPE pellets are introduced into the system via powder injection system where a carrier gas is used to carry the aerosol in to the plasma zone.
In the first step of the arc discharge, carbon vapor composed of atomic species and very small clusters is produced by the sublimation of carbon in an inert atmosphere through an electric arc maintained between two electrodes. In a second step, the carbon vapor is expended in an inert gas. In a third step, the carbon vapor is quenched and a part of the small clusters self-assemble to produce fullerenes.
Use Case 3 - Biogas as Feedstock
The methods of producing Hydrogen from Biomass can be broadly classified as physicochemical, thermochemical, and biochemical. Plasma can contribute to the thermochemical route by driving pyrolysis, gasification, and reforming (biogas). In this case, biogas reforming is like the dry reforming of methane except for the difference in feedstock composition, i.e., the methane-to-CO2 ratio of biogas is below the stoichiometric ratio of typical dry reforming.
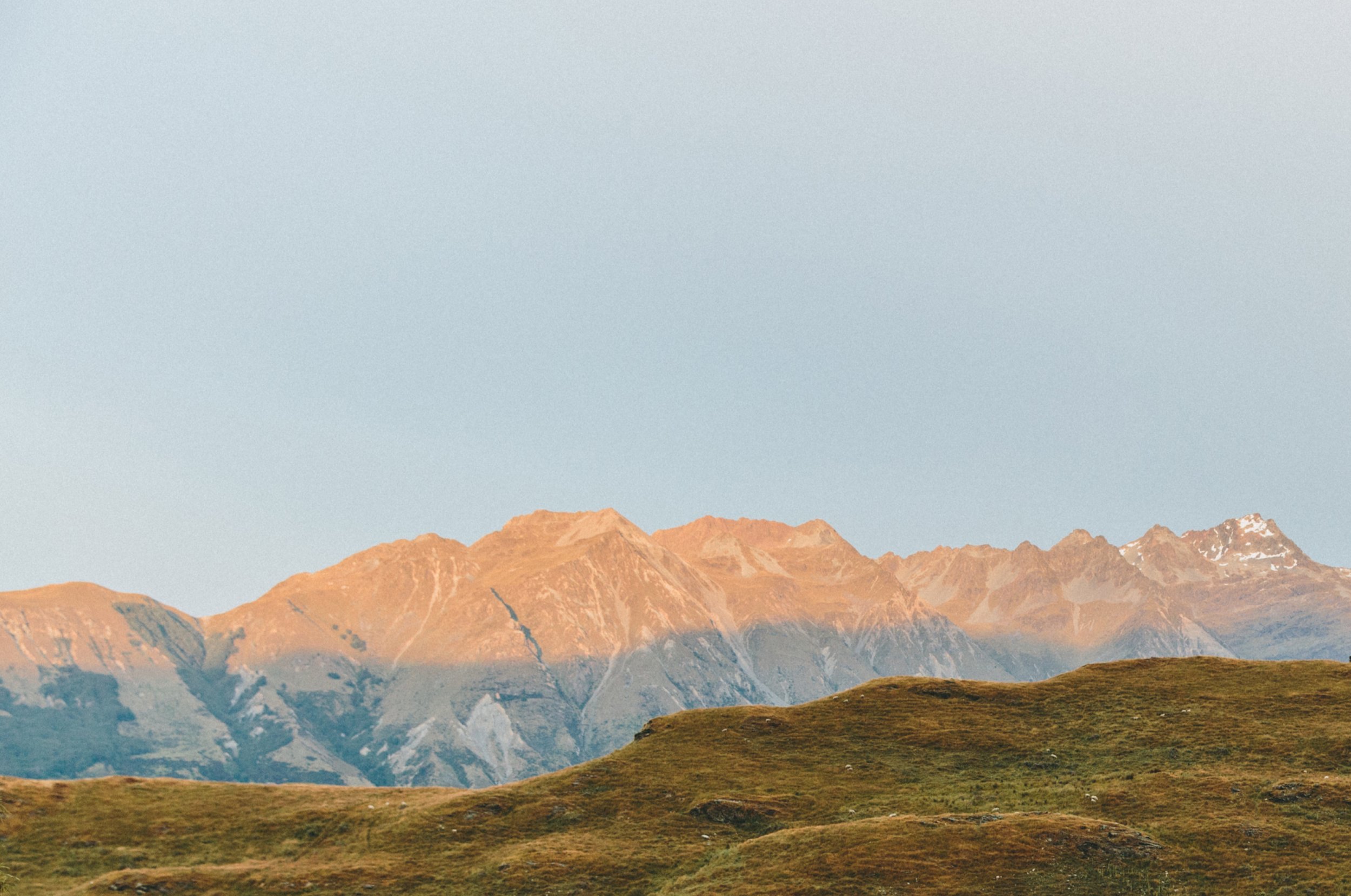